If you‘re planning on remodeling or modifying your manufactured home, it‘s important to understand how they‘re constructed. This will save you from making costly mistakes regarding design and material choices.
For example, when renovating the flooring or interior walls, you’ll need to have the structure know-how of your modular home or the mobile home design. Understanding the order in which the house was built may aid you in better planning your remodeling.
If you don’t have all of the facts, renovating modular homes can be a nightmare, but it can also be a breeze if you know what you’re doing.
How Are Double-Wide Mobile Homes Built?
One of the top trends in home remodeling is to make a manufactured home feel more like a traditional site-built home (improve the mobile home living experience). This can be accomplished in various ways, ranging from changing the room layout to adding unique features and finishes.
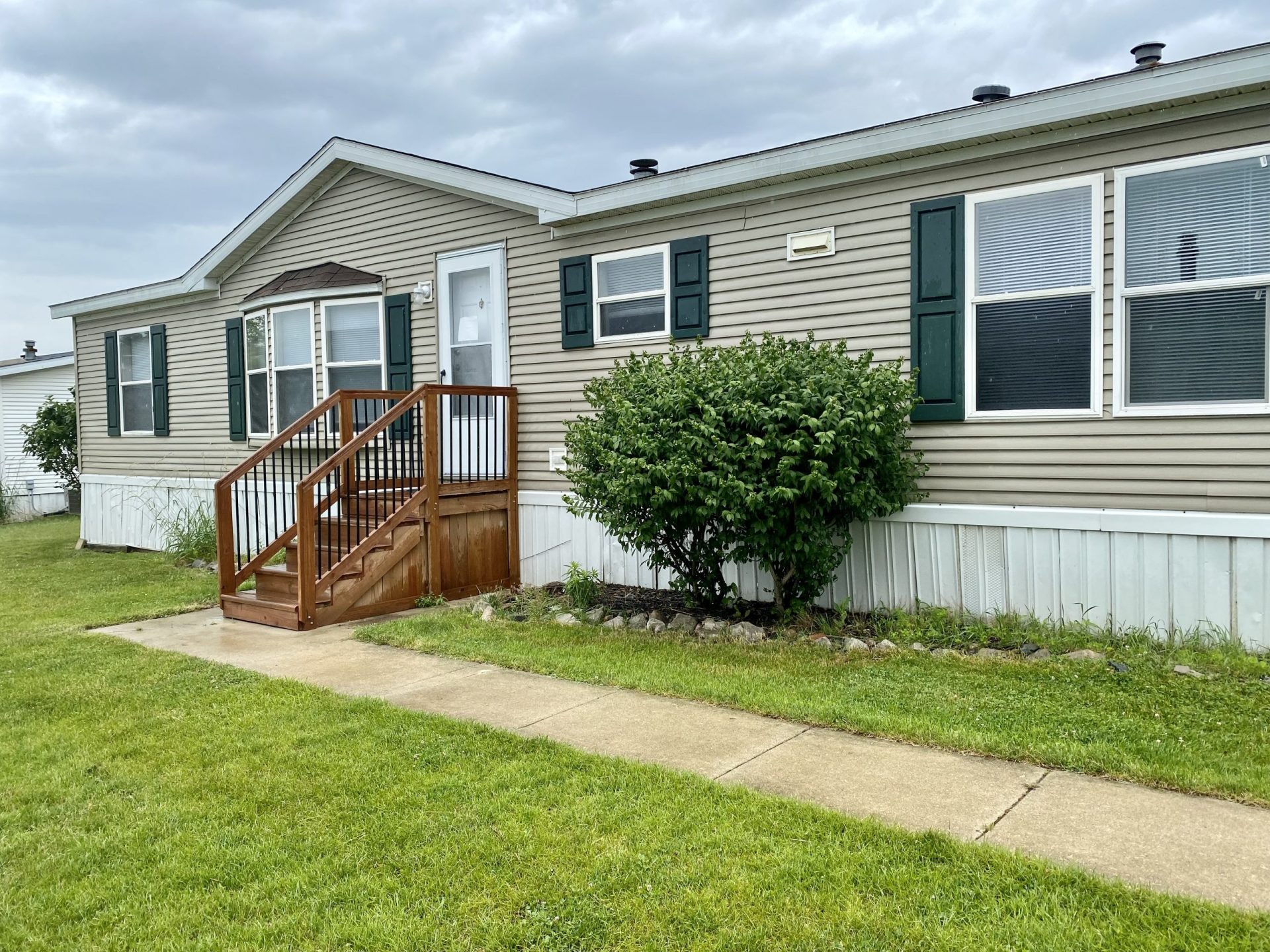
With that said, in this article we will look at the different steps it takes to build a double-wide home.
What are Double-Wide Homes?
What is a double-wide manufactured home? Double-wide mobile homes are built in factories and transported to the site. A double-wide manufactured home has a width of 20 feet or more and must be transported in two pieces. It is built to be almost twice as wide as single-wide mobile homes. This extra width provides room for an extra bedroom, bathroom, and larger living space.
A double-wide manufactured home is built similarly to a single-wide manufactured home, with one exception. The double-wide manufactured home requires two trailer sections to be pulled up together, while the single-wide manufactured home only requires one.
What Materials are Used to Build Mobile Homes?
Before we get into the details of the manufactured home construction process, it’s necessary to understand the used materials.
While there are several materials used in the building process, the following are a few examples:
● Electrical wiring
● PVC or chrome plumbing
● Wood flooring
● Fiberglass insulation
● Lumber framing
The sole difference between a modular home/mobile home vs. stick-built homes is that mobile homes acquire their materials in bulk and, thus, receive substantial discounts, whereas traditional homes do not. This savings is then handed down to the mobile home buyers, which is a big part of the lower cost.
With that in mind, let’s look at how manufactured homes are constructed.
Everything Begins with a Strong Foundation
The manufactured housing industry was not always as popular as it is now. Quality improvement and energy-efficient manufactured homes are the things that have revolutionized the game.
Today’s mobile homes are built with a lot more care and attention to detail than they were in the past. With that said, a solid foundation is the catalyst of any long-lasting house. A manufactured home is constructed in a factory, implying that it is subject to stringent building regulations.
Since a manufactured home is essentially a modular construction, there is no waste of materials. As the carpenter’s adage goes, “measure twice, cut once,” which is a perfect way to describe the manufactured home building process.
As a result, the foundation of your home has been carefully planned (construction methods) and built to maintain the stability and integrity, which helps the overall life expectancy of a mobile home.
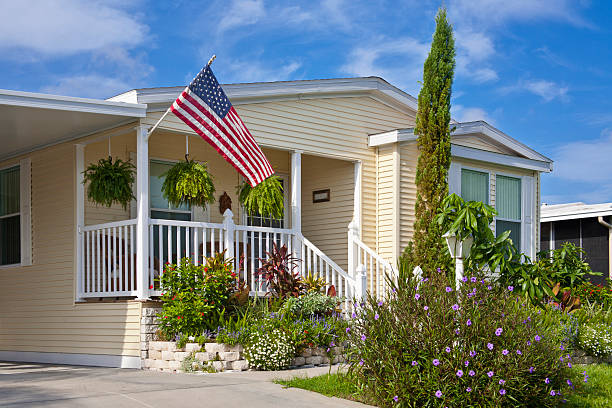
Typically, manufactured homes begin with a steel I-beam frame that will support all of the weight when it is completed. After the frame has been welded together and stabilized, decking and a thin layer of concrete can be applied. Single-wides and double-wides are both supported by steel chassis.
When this process is finished, the foundation is ready to support the weight of the mobile home framing, roofs, and other features that will be built on top of it. Not only must the foundation support the weight of the house, but transportation also poses a significant risk to the structure; thus, it must withstand the strain.
Constructing the Walls and the Roof
When it comes to putting up the walls, a lot has changed. As a result, instead of paneling or wood, drywall is commonly employed as an interior wall these days. Not only does it provide better insulation, but it also give the mobile home more of a traditional stick-built home look.
Each module is created individually and can be simply linked as needed, allowing for the speedy building of mobile houses. As a result, the walls, roof, and floor are all constructed individually and require some assembly, with the inclusion of features like BA-ALR-12 Aluminum Recessed Access Door enhancing functionality.
At this stage, it’s a careful balance between squeezing in walls and making the foundation secure. Walls follow the layout on foundations, and screws are used to make them firm (attached to floor joists).
Once this is complete, it’s time to run the electrical wires, do the plumbing lines as needed, and finish off with insulation and drywall, sheathing, and sealants. From here, it won’t be long before the mobile home takes on a pleasing appearance.
Time to Put Everything Together: Utility Hookups and Home Siding
Mobile home construction is a complex process that requires many specialized skills. Frame carpenters, cabinet makers, plumbers, electricians, roofers, insulation specialists, and more are all needed to complete the job successfully.
Since each stage (flooring, roofing, vinyl siding, etc.) of mobile home construction is assigned to certain individuals with specific skill sets, the majority of the work may be done simultaneously. At this point, doors and windows are also added.
Time for Quality Control
Supervisors frequently monitor mobile home construction quality practices to ensure that high standards are maintained according to federal government regulations (HUD Code for manufactured homes). Inspectors are also commonly used to inspect the finished product.
All mobile housing-related policies are governed by the Department of Housing and Urban Development (HUD), which has many standards and regulations.As a result, these third-party inspectors guarantee that the home meets the HUD requirements during the building process.
If the home fulfills the needed criteria, it is released to the manufactured home buyers; if not, alterations are done until it is code compliant. Check out how manufactured homes are constructed in more detail here (Clayton Homes).
Transportation and Installation
It’s time to transfer the structure to the site location, where it’ll be laced atop the foundation once it’s up to code. Since it’s a double-wide home, it’s shipped in two sections, which are then assembled at the foundation site.
Transporting a mobile home is a huge responsibility. A trailer truck can be difficult to steer, and a driver who is not experienced in this type of vehicle could cause irreversible damage. For that reason, the safest and most reliable way to transport a manufactured home is with the help of professional drivers.
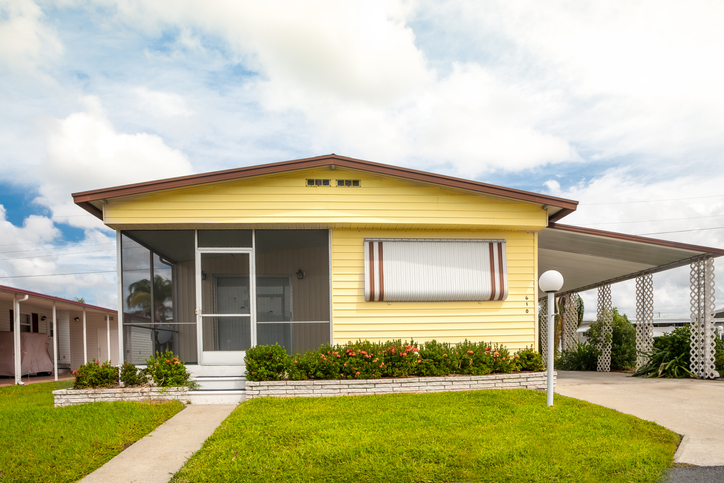
When the home arrives at the job site, it is set on its prepared foundation, which could be an excavated basement, sturdy stem walls, or pier-and-beam foundation.
The next stage is to link the house to anchors, used to secure a building or other structure to the ground. They are built to withstand wind and water pressures to keep the home from overturning, sliding, or rising.
The home is also connected to on-site water plumbing, electrical lines, and heating and cooling during the installation process. After the installation is complete, a home inspection is performed to make sure everything is up to code and verify there were no improper installation practices.
Things to Know Before Buying a Manufactured Home
Manufactured homes are popular in today’s society because they are cost-effective, offer a variety of amenities, and are transportable.
There are numerous things to consider when buying a mobile home. You should know how much it will cost to maintain the manufactured home, how long it will last, on average, and what you can do if you need to sell it.
With that said, here’s what you need to know before rushing to find manufactured home builders.
Quality and Building Standards
All manufactured homes are subject to the HUD Code. The HUD Code was established in 1976 to address the quality standard of manufactured homes (energy-efficiency, safety, etc).
The code is updated and revised every few years, and is enforced by the Department of Housing and Urban Development. This establishes mobile homes as secure structures capable of giving you the same benefits as site-built homes.
The high-quality materials utilized in today’s manufactured homes make them safe. Fire rated interior paneling, for example, is used to protect the home from hazardous conditions.
Defining Your Home
When you live in a manufactured home, you sacrifice square footage for mobility; this means that your home will be smaller than a traditional home – but not by much. Nevertheless, these homes typically can be built in sizes ranging from one bedroom to five bedrooms.
Consider asking yourself the following questions before buying a manufactured home.
● Who is going to live there?
● How many bedrooms are needed?
● Is a home office a necessity?
This will allow you to make the most of your living area.
This is also the time to decide on any customizations and speak with your builder. For instance, do you desire granite countertops or do you want something else?
Choose Your Mobile Home Location
Before buying a manufactured home, decide whether you want to place your home in private land or in mobile home parks.
Each choice has both advantages and disadvantages, so examine them carefully before selecting. If you like the idea of living in a community/trailer park, visit a few in your desired location, talk to various park owners, and take tours to help you decide.
Great manufactured home communities can be found in cities like Fenton, MI and Grand Rapids, MI, just to name a few.
Mobile Home Financing
Before rushing to purchase a home, it’s equally crucial to understand the financing side. You must be aware of your alternatives, which are not as many as those available in typical houses. With that said, if you place your home on private land (permanent foundation), you may have a better chance of getting traditional financial institutions to fund it.
The following are some of the ways to finance a manufactured home:
● FHA Loans
● Chattel Loans
● VA Loans
● Personal Loans
Frequently Asked Questions
Manufactured homes (factory built homes) are the most common form of unsubsidized affordable housing in the U.S. because they’re the cheapest on the market. So here’s what people are asking about manufactured homes:
Are Double-Wide Homes Worth the Money?
A double-wide home is an excellent way to save money (affordable homes) while still giving you and your family the space you need to live a full and active life. It’ll be a fraction of the price of a stick-built home.
How Long Does a Double-Wide Trailer Last?
According to the U.S. Department of Housing and Urban Development (HUD), a double-wide home can last between 35 to 50 years, depending on how well it is maintained.
Why are Double-Wide Homes so Cheap?
They are mass-produced and erected on assembly lines.
Can You Remove Walls in a Double-Wide Mobile Home?
Yes! You can remove the interior and exterior walls of a manufactured home so long as they are not load-bearing.
What are Mobile Home Wall Panels Made of?
Vinyl-on-gypsum (VOG) panels, rather than ordinary drywall, are commonly used in manufactured homes. With that said, drywall in mobile homes is becoming more and more popular.
Final Thought
A double-wide mobile home is a great way to downsize without sacrificing too much space. The living area in these double-wide homes is typically larger than many apartments, and the lot size required for placement is significantly smaller than what is required for most stick-built homes.